This article is a continuation of: "An Introduction to Implementing Predictive Maintenance in Manufacturing with Azure AI"
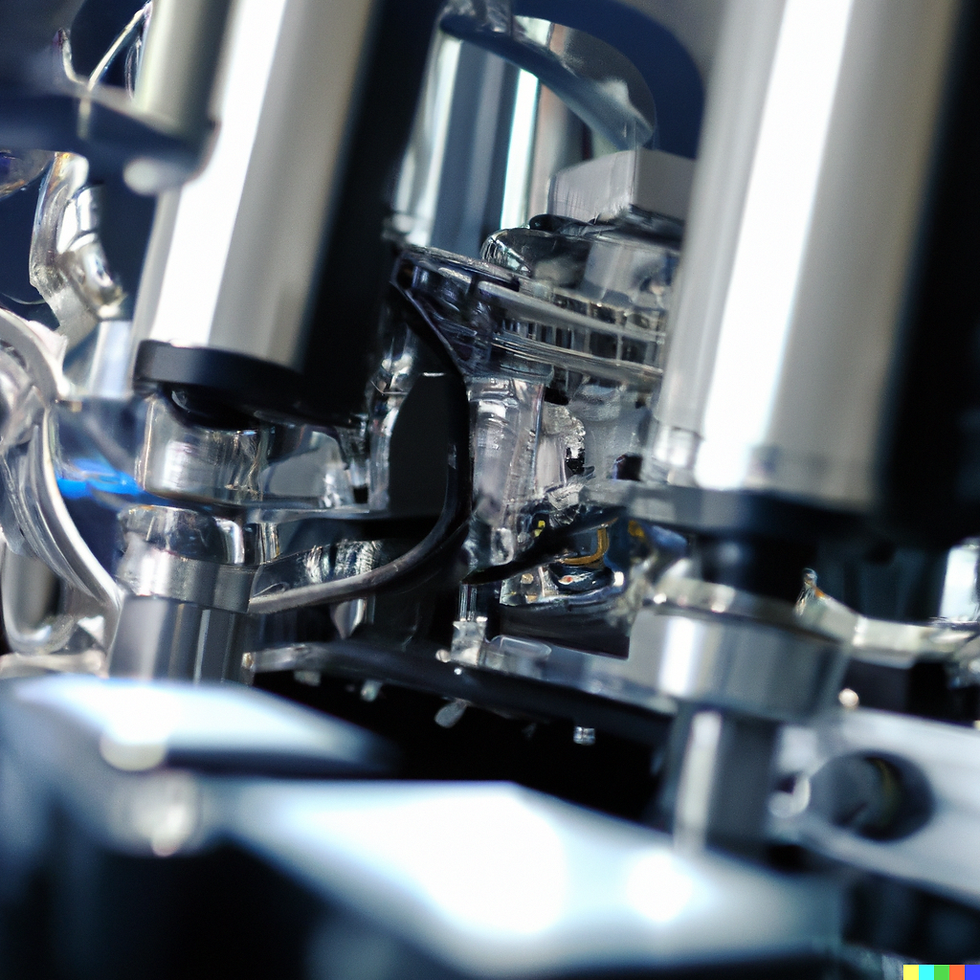
Before utilizing AI and ML for optimizing operations within a manufacturing plant, the first thing that must be done is the selection and installation of sensors on the machinery. These sensors will provide the data necessary for analysis and modeling.
Below is an outline of sensor types and how they can be utilized for preventative maintenance.
1. Temperature Sensors:
Role in Predictive Maintenance: Temperature sensors monitor the heat levels of critical components. Elevated temperatures can indicate overheating, excessive friction, or problems with cooling systems.
Use Cases:
Detecting overheating in electric motors, which could lead to bearing failures.
Identifying abnormal temperature spikes in engine components, signaling potential issues.
Benefits: Early detection of temperature anomalies allows for preventive actions such as adjusting operating parameters, scheduling maintenance, or replacing components before catastrophic failure occurs.
2. Vibration Sensors:
Role in Predictive Maintenance: Vibration sensors detect oscillations and vibrations in machinery. Changes in vibration patterns can indicate misalignments, imbalances, wear, or impending bearing failure.
Use Cases:
Monitoring the vibrations of rotating equipment like pumps, compressors, and turbines.
Identifying unbalanced loads in conveyor systems.
Benefits: Vibration analysis helps diagnose issues with rotating equipment, preventing catastrophic failures and optimizing maintenance schedules.
3. Pressure Sensors:
Role in Predictive Maintenance: Pressure sensors measure fluid pressure within systems. Abnormal pressure readings can indicate leaks, blockages, or system inefficiencies.
Use Cases:
Detecting leaks in hydraulic systems by monitoring pressure drops.
Identifying clogs or obstructions in pipelines by monitoring pressure changes.
Benefits: Early detection of pressure anomalies can prevent system damage, reduce energy consumption, and minimize production downtime.
4. Ultrasonic Sensors:
Role in Predictive Maintenance: Ultrasonic sensors are used for detecting high-frequency sound waves generated by equipment. They can identify issues like air or gas leaks, steam trap failures, and electrical faults.
Use Cases:
Locating compressed air leaks in pneumatic systems.
Detecting partial discharge in electrical equipment, which can lead to failures.
Benefits: Ultrasonic sensors enable the early detection of issues that are not visible to the naked eye, reducing energy waste and preventing equipment damage.
5. Current and Voltage Sensors:
Role in Predictive Maintenance: Current and voltage sensors monitor electrical parameters. They play a crucial role in monitoring the health of motors and other electrical components.
Use Cases:
Detecting overloading in motors by monitoring current spikes.
Identifying voltage fluctuations that may harm sensitive equipment.
Benefits: Monitoring electrical parameters ensures the safe and efficient operation of electrical equipment, reducing the risk of electrical failures and fires.
6. Infrared Sensors:
Role in Predictive Maintenance: Infrared sensors detect temperature variations across surfaces. They are used for identifying hotspots or abnormal heating in electrical systems, machinery, and building infrastructure.
Use Cases:
Locating hotspots in electrical switchgear and panels.
Detecting overheating bearings in rotating equipment.
Benefits: Early detection of temperature anomalies helps prevent electrical fires, equipment damage, and unscheduled downtime.
Each type of sensor provides unique data that, when analyzed in real-time or over time, can reveal patterns and deviations that signal potential issues. The integration of data from these sensors into a predictive maintenance system allows for proactive maintenance actions, reducing downtime, minimizing repair costs, and improving overall operational efficiency.
Comments